News
03-11-2015
Production of Bio-aromatics from Organic Waste and Domestic Waste
It will be clear soon how the processes devised for the production of bio-aromatics from organic waste and domestic waste are progressing on the laboratory scale. The first calculation of the returns and the cost can also be made at that stage. Biorizon business manager Joop Groen and Marcel Ligter, process technologist at Attero, are confident that these processes can be profitable.
Composting and fermentation are valuable processes for reusing organic waste. However, some of the biomass supply can also be utilised for other processes that add even more value. That is the vision of the Dutch waste sector, which intends to further develop into a raw materials supplier.
In the Waste2Aromatics project, three waste companies (Attero, AEB Amsterdam and Orgaworld), along with the Waste Company Association and initiator Biorizon, are investigating how they can substantiate that vision. Biorizon is an initiative of TNO, VITO and Green Chemistry Campus.
Organic Waste
The first step in the project is defining waste types that are suitable as supply for the reactors where sugars are extracted from the biomass. ‘The biggest flow by far is organic domestic waste, but there are still numerous other, more defined flows, which can be suitable candidates due to their components such as sugar and/or cellulose and hemicellulose,’ asserts Marcel Ligter, process technologist at Attero. ‘Together with the other waste processors, we have specified a list of nine flows based on our expertise in waste processing. This includes waste from street sweeping and orange peels. In the laboratory we have analysed those nine flows, into which I am not allowed to provide further insight out of competitive considerations, for organic dust content, sugar content, and particle size. Parameters which we think are important for the assessment of whether said waste is a suitable basis for the eventual production of bio-aromatics.’
Based in part on those analyses, a short list of three waste flows was decided on, and the Biorizon process technologists have meanwhile begun to work on this. The project participants do not want to name the three flows in concrete terms here either. It should be clear that organic waste will certainly be included, because of its magnitude alone. Fractions rich in cellulose will also be researched further.
Two Ways
Before you can actually start production of bio-aromatics, sugars and cellulose in the waste flows must be converted into furans. These are compounds from which bio-aromatics can be made. ‘We have two technologies available for that conversion, the use of which depends on the waste flow to be processed,’ explains Joop Groen. ‘The first one is SHS, “super heated steam”, a technology patented by TNO that involves having super-heated steam pass through the biomass. This works well for biomass with a high dry dust content, also known as solid biomass, for example straw and organic waste. We can efficiently convert cellulose and/or hemicellulose into sugars in the reactor. Moreover, you do not have to stop there, because with the right catalyst you can also convert the sugars into furans. We are currently sorting out this interesting possibility on a small pilot scale of approximately one kilogram per hour. The challenge here is that specific sugars are converted into different furans, so you must make sure the reaction does not go too far. If that were to happen, we would lose the reactive ring we sorely need to produce the desired bio-aromatics in the last step of the process.’
SHS is not suitable for the wet fractions. We work with a two-phase system at Biorizon instead. It starts with an aqueous solution in which the sugars dissolve well and the reaction can take place. The reaction will continue to proceed properly if the reaction product is output to the second phase, the organic one. ‘To present we have experimented with this system on a small scale, in a microwave reactor system. Meanwhile we are building a bigger test system, on a scale of up to 10 litres per hour,’ says Joop Groen.
Windfall Functionalities
A complete pilot chain, from sugars to bio-aromatics, will eventually be built at the Green Chemistry Campus, where upscaling takes place. ‘That is to say, with the furans you haven’t gotten to the bottom of it yet. You need a downstream processing unit to purify those products, and reactors to convert those intermediary furans into the desired platform furans, which must subsequently be converted into the bio-aromatics in another reactor,’ says Joop Groen.
Considering all those steps, each of which has to be optimised and upscaled individually, Joop Groen cannot yet comment on commercial opportunities at this time. ‘We are striving to be able to run one or several large-scale processes by 2020. From the market’s point of view, I can argue that we have more opportunities with the specialties than with production of relatively low-functionality bulk aromatics such as benzene and toluene. Our raw materials give us a slight advantage over the petrochemical industry, since the functionalities are windfalls, so to speak. Look at the structure of sugars. They contain hydroxyl groups, which are suitable for many things. Efficient use of the functionality available offers you good opportunities in the market of functionalised aromatics, the specialties, where the volumes are furthermore lower and the prices higher.’
Raw Materials Strategy
The chance of success is closely related to the capacity of efficiently obtaining one or several homogeneous raw materials flows from the heterogeneous waste flow that can be processed on a large scale. Ligter: ‘We made a first selection by deciding on three candidate waste flows. Each of these flows still requires a number of pre-processing steps before they can be brought into the reactor. Consider organic waste alone, which consists of approximately 30% organic material, but for the rest contains a lot of water and sand. From our expertise on using organic waste in fermentation and composting, we already control those steps properly, but other flows, especially the smaller ones, still require the necessary development work. The efficiency of organising collection and processing also plays a role in those small flows.’
Green adds: ‘A sound raw materials strategy, i.e. finding those raw materials that provide the best result for your money, is just as important as optimising the return, producing as much of the final product as possible per kilo invested. The combined expertise of the waste companies and the process technologists in the Waste2Aromatics project enables us to take optimum advantage of this combined action between raw materials properties and process parameters.’
Shared Research Center
Biorizon, an initiative of TNO, VITO and the Green Chemistry Campus, strives to bring together companies active in the fields of raw materials, conversion, equipment, intermediary and final products in the world of bio-aromatics. This takes place in a community and the Shared Research Center (SRC) at the Green Chemistry Campus in Bergen op Zoom, the Netherlands, where parties cooperate in various projects, including Waste2Aromatics, according to the innovation method. Interested companies can join the SRC and the community.
Source: the highly recommended international version of Agro & Chemistry
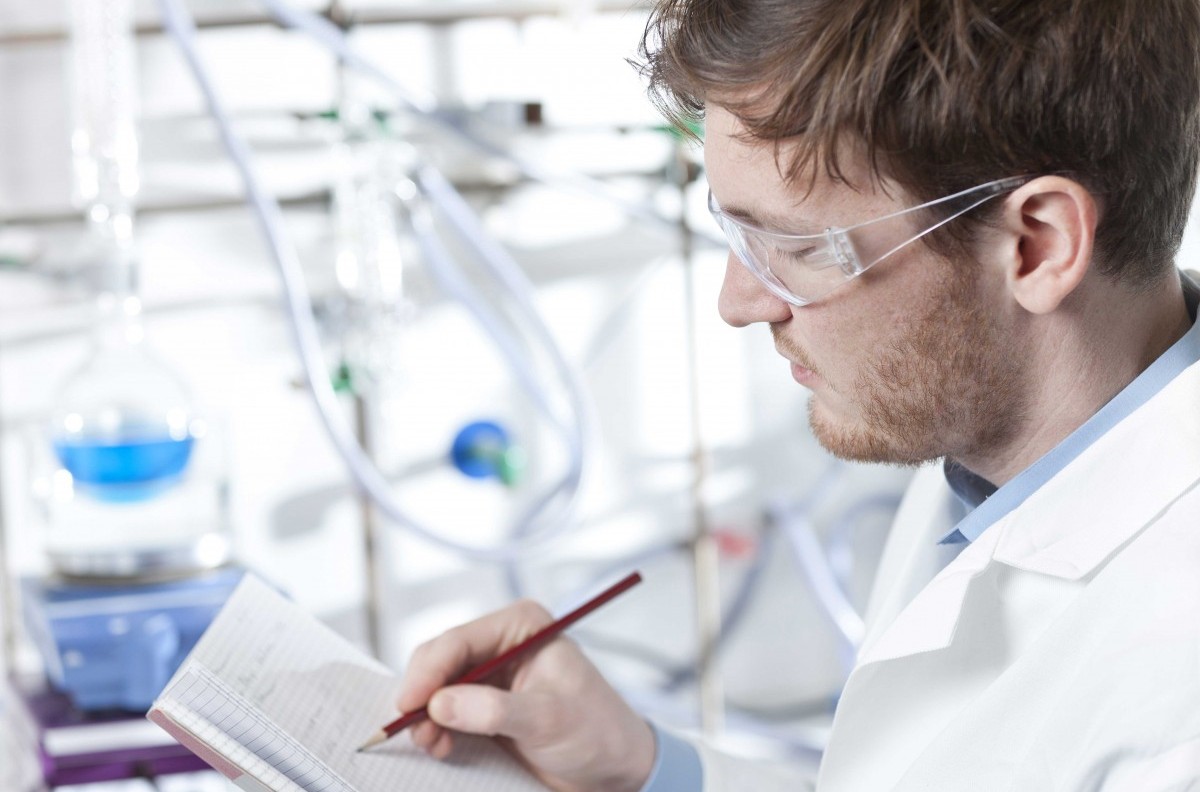