News
05-10-2015
Lignin as raw material for asphalt and roofing
Put a chemist and road-builder together and you have an explosive mix. Not in the sense that there is a danger of explosion but in terms of power and knowledge. By joining forces in the laboratory, Dr Ted Slaghek and Dave van Vliet of Biorzion co-founder TNO created a type of bitumen with improved properties. Based on lignin.
Aromatic ring structures
A sustainable economy requires alternative raw materials. After cellulose, lignin or wood is the most common organic material on the planet. The interaction of cellulose, hemicellulose and lignin generates a composite that gives wood its strengths. Industry is familiar with lignin mainly as a waste material from the production of paper, removed from the pulp with sulphurous chemicals in the Kraft process and then on to the incinerator to generate energy for its own production process. Or it makes its way to other manufacturers as a binding agent for asphalt or concrete. As long as lignin contains sulphur, its application is limited, which is a shame given its aromatic ring structures that are seldom encountered in nature but can be applied in a whole range of areas, for instance as a fully-fledged – green – raw material for asphalt and roofing. Currently, bitumen is used for this but, as a by-product of petroleum, this is not sustainable and neither is its availability unlimited, something from which lignin does not suffer.
Superlignin
TNO has come up with various ways of making lignin available virtually sulphur-free, as in a creative process whereby enzymes break down the cellulose into glucose. Dr Ted Slaghek is senior specialist at TNO in the field of lignin. He explains: "In Zeist we have a research group that works on drying. Superheated stream has been used there for decades to bake fries, dry mealworms, roast cocoa, and so on. A few years ago we thought that we could do more with this method and so we hit on the idea of treating straw with superheated steam. Instead of using 100% sulphuric acid, as in the biosulfurol process, we used just 0.5%. We were astounded how well it worked. The lignin we got from that straw is superlignin! Highly molecular, mildly treated and with no bad odours."
Source: TNO
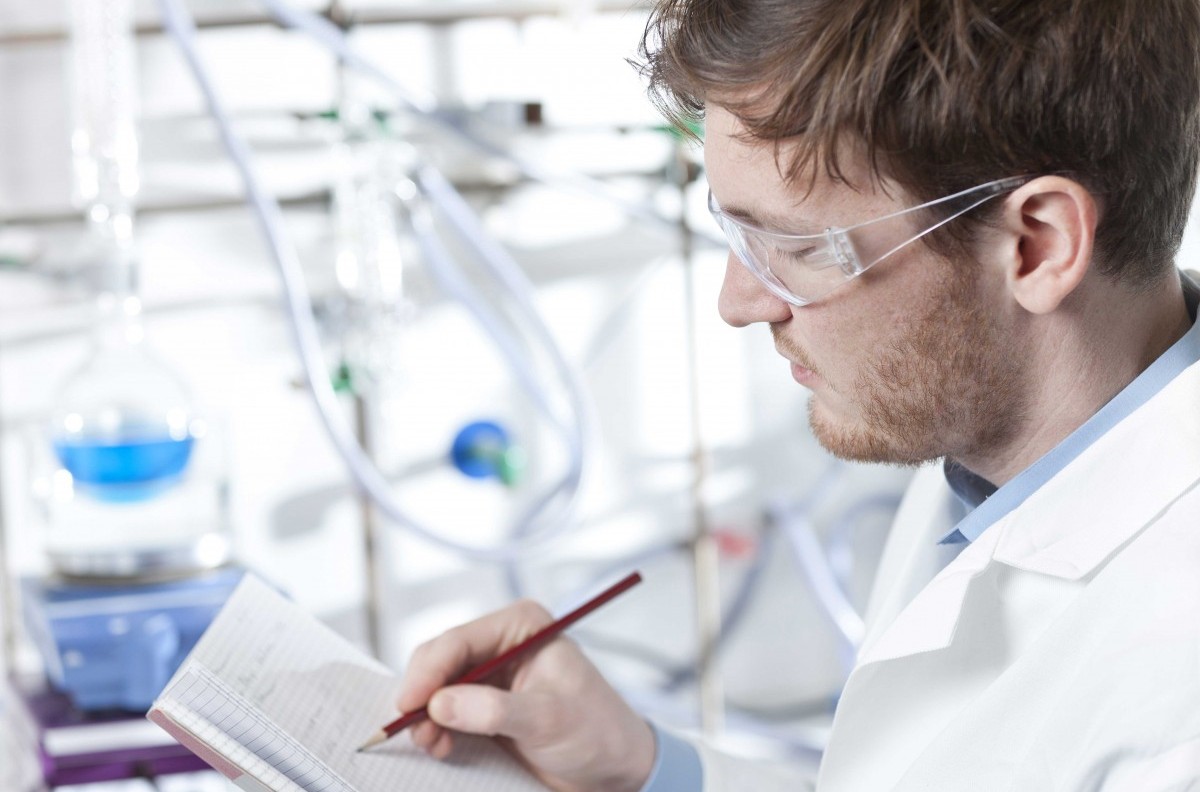